From "15 days" to "7 days"
"For a project design like this, it usually takes about 15-20 days, but this time I was given less than 7 days," Engineer Li, the R&D manager responsible for product design in this project, felt that the time was really tight when he received this task. Despite this, in order to meet customer needs, Sanco had to win the race against time, and the first person to take the baton was Li Gong and his R&D department.
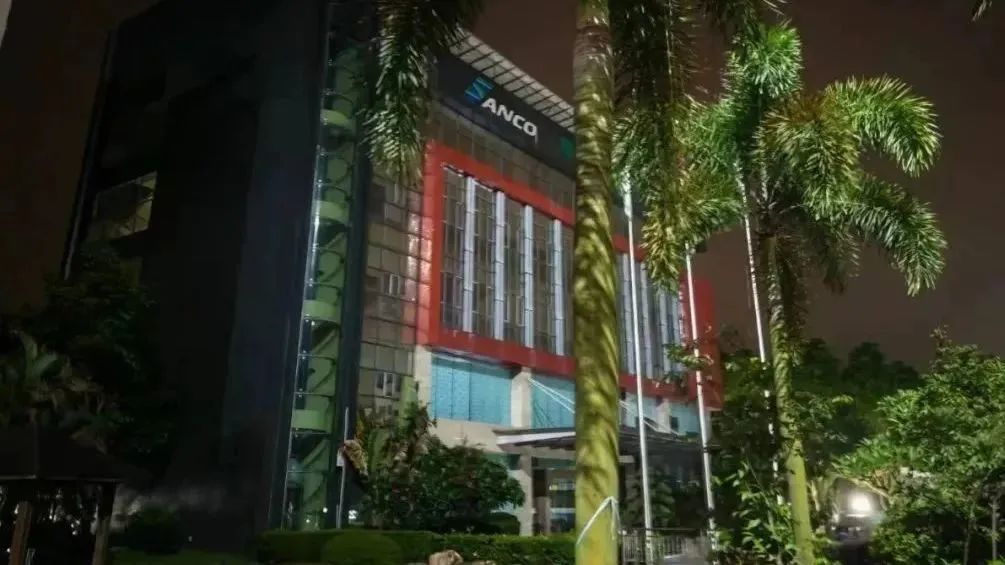
"No matter what time you call, there will always be someone to answer."
As a planning engineer in the mold department, Engineer Xue's main job is to coordinate internal and external resources, monitor project timelines, etc. However, the project he received this time is the tightest schedule he has encountered since joining Sanco over a year ago, which added extra pressure on him. Considering that there are many mold parts involved in this project, they decided, after internal discussions, to adopt a "zero-waiting" work mode, meaning that after each process is completed, the next process is started immediately.
In order to minimize the waiting time for each process, Xue not only needs to communicate and solve on-site issues internally at any time but also needs to schedule the time of external suppliers. Because of the large number of parts and the tight schedule, a small part of the mold department outsourced the production to suppliers, and sometimes the suppliers even arranged for delivery three times a day to meet the schedule. When confirming the delivery time with Xue, they would ask if someone would be available to receive the goods if they were delivered in the early morning. His answer was, "No matter what time you arrange for delivery, as long as you call me, I will definitely be the first to receive it."
Therefore, during the project development period, at midnight, 2 a.m., 3 a.m., Xue received delivery calls, and he never delayed a single time. He immediately arranged for colleagues to receive the goods, and once the production colleagues in the workshop received the goods, they would inspect them immediately and start assembling without delay. With such close cooperation and overtime work, the mold department truly achieved "zero-waiting" in the project development process.
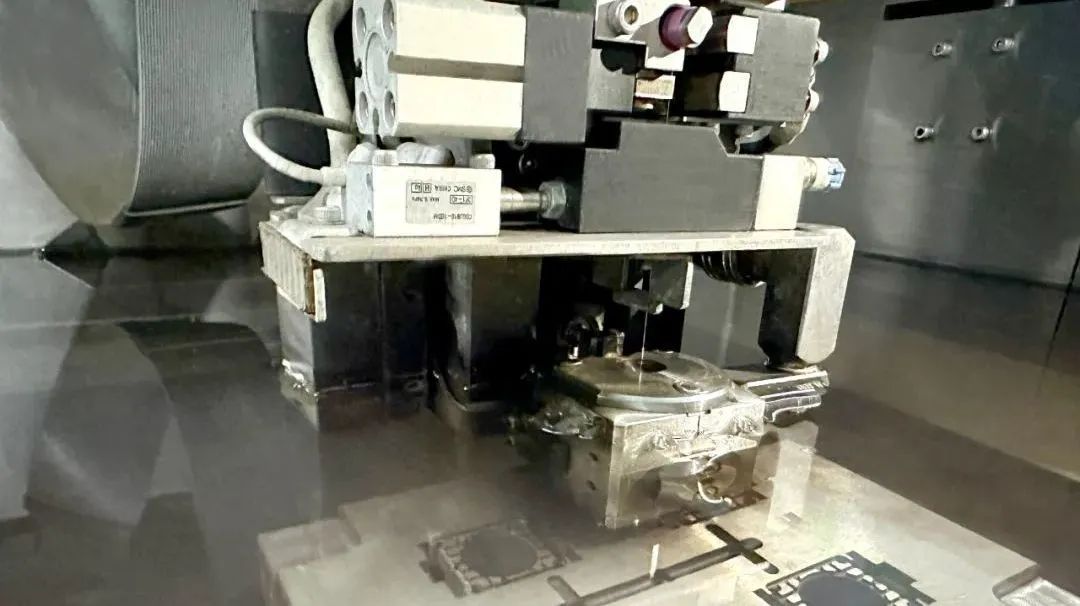
Three business trips a week
As the core component of the connector, the importance of terminal performance is self-evident. For R&D supervisor Hu, the main difficulty in the development of this connector terminal lies in production manufacturing and quality confirmation. "This terminal is composed of beryllium copper and phosphor bronze. The processing steps for beryllium copper include wire cutting, bending, electroplating, etc., while the processing steps for phosphor bronze include wire cutting, CNC, bending, electroplating, and then these two parts are riveted and bent together," project procurement manager Deng listed out the processing technology of the terminal in one go. With these complex processing steps, if one step goes wrong, they have to start all over again, so they need to closely monitor every aspect of the terminal processing.
Therefore, in the span of one week, Hu and Deng visited the manufacturers processing the terminals three times, with the last visit even involving staying up all night with the company's master craftsmen and boss. On that night, besides them, there was also Li Xueguang, who arrived at the scene from the mold department after successfully testing the product, to match it with the terminals in production. Anxious, tense, excited, and various complex emotions lingered in the hearts of the three individuals, until finally, in the early hours of the morning, they obtained the qualified terminals, and the tension in their hearts finally eased.
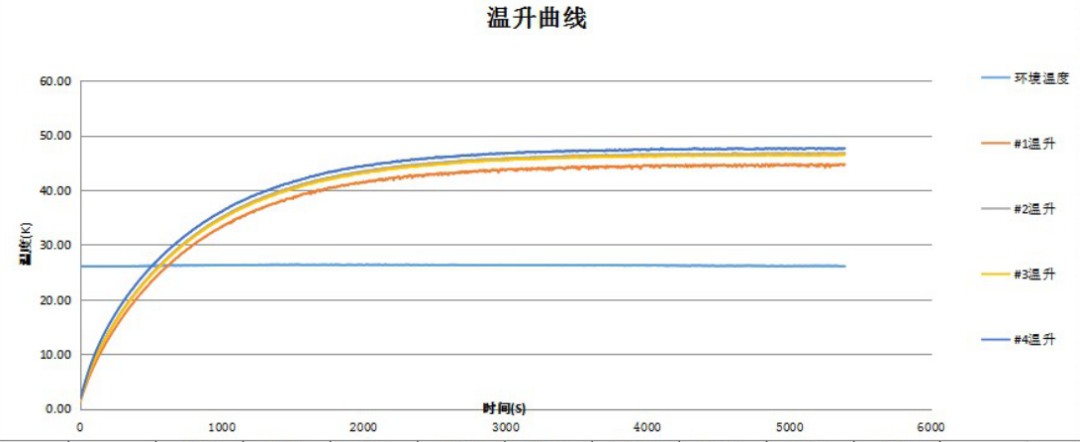
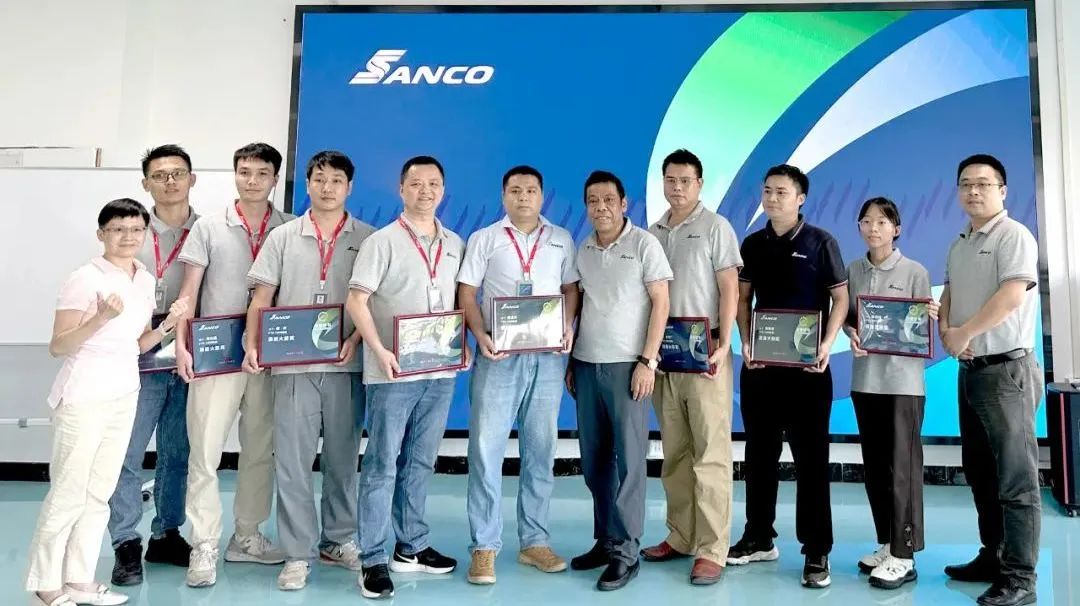
Putting aside other tasks at hand, actively assisting project team colleagues who are rushing to meet deadlines; in order to communicate requirements with suppliers more meticulously and accurately, even if there are already tasks arranged, adjusting time to go to the site together with procurement colleagues; not only focusing on the progress of their own department's work, but also constantly confirming and keeping track of the R&D progress and timeline of the previous process... As Deng put it, it is because every person in the team has put in their utmost effort that success can come on time!